Over the past nine years, the Topflight Travel Group has adopted Lean practices, inspired by Toyota, the global leader in Lean methodologies.
By prioritising continuous improvement and waste elimination, Topflight has significantly boosted its operational efficiency. Just last week the company reported a 42% increase in revenues and a 59% rise in operating profits for the last financial year, surpassing pre-COVID figures from 2019.
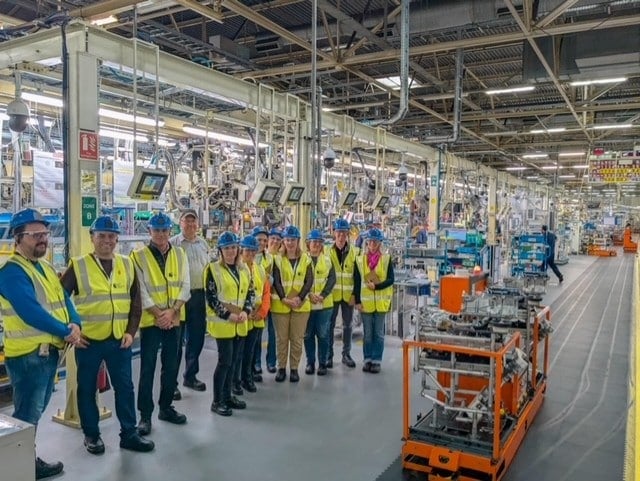
While the hospitality and service industry differs significantly from manufacturing, the Toyota Lean Management Centre based in Deeside in North Wales demonstrates how Lean concepts can be effectively applied in non-manufacturing sectors. By sharing best practices rooted in the Toyota Production System, the Centre has equipped organisations like Topflight with the tools needed for success.
Last week, Topflight’s senior management team took part in a two-day intensive training course at the Toyota Lean Management Centre in North Wales. This immersive experience offered valuable insights into how Toyota integrates Lean principles into every aspect of its operations, regardless of staff seniority. This company-wide mindset fosters a culture of continuous improvement and efficiency and every employee has their part to play.
Michelle Anderson, Marketing Manager at Topflight, commented: “The principles established by Toyota’s manufacturing approach have allowed us to enhance every aspect of our tour operation, ultimately benefiting both our customers and travel agent partners. Our focus on analysing and streamlining processes helps us minimise waste—be it time, materials, or resources—and continually refine our operations and ensure that every activity undertaken is adding value to the customer.”